« Senshafuda Project - final package design | Front Page | Breaking News ('slightly' edited) »
Senshafuda Project - We have liftoff! (and ready for orders)
Posted by Dave Bull on April 24, 2011 [Permalink]
Continued from the previous post in the thread | Starting point of the entire thread is here
Ladieeeeeeeees and Gentlemen!
After ten weeks of planning and preparation (has it really been that long?), we have now successfully launched our little print series. Proofing with Tetsui-san yesterday was very successful, and we came up with what I think is a very nice set of prints.
You can see them on their order page here, where the blue 'Add to Cart' button is now active!

With just the two of us there this time, the proofing was definitely more peaceful. And with the basic concept sorted out from the previous session, our work this time was focussed on getting the colours adjusted so that they would work together, and sorting out some problems getting the impressions smooth (as usual, the wood is not what it 'should' be, and although there are no obvious defects in it (knots, etc.) there are places where the grain insisted on coming out in places we didn't want it).
Here are a few snapshots:
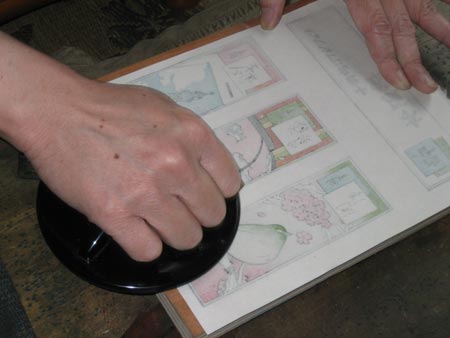
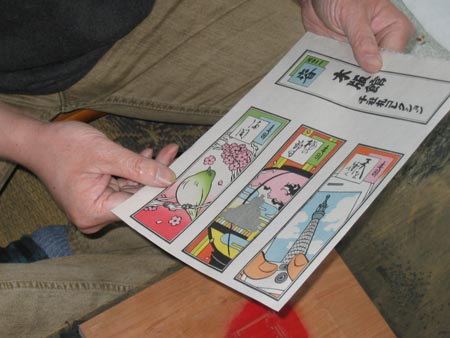
We had six sheets in the batch - kind of a 'mini' print run - and adjusted tones up or down to give us some variation for comparison.
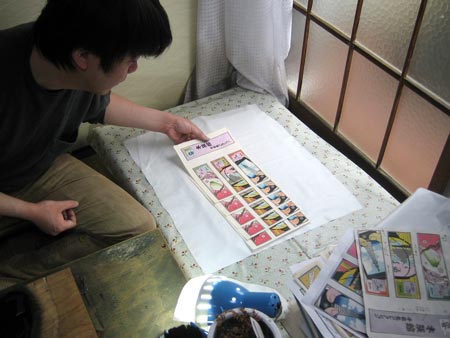
At the end of the day, we agreed on which particular tones were the best, and I left the new 'master copy' with him to be his guide when he starts printing the first batch. That won't be tomorrow, as he is still working on a job for the craftsman's association - an edition of 100 Hiroshige reproductions from the 'Famous Places of Edo' series that they publish. He said that this would take him to the end of the week, and he'll then get started on our senshafuda.
Just how long it will take him is not quite clear. If it were me, I would do around 100 first, in order to get some out the door as soon as possible, and then do the second 100. But he would rather work the entire batch of 200 at one time, in order to maintain best consistency. That'll mean of course that none can be shipped until the entire batch is ready (a two-week job at minimum), but no complaint - at this point, he's the boss on the printing job, and the only concern is to get them done properly. We've all waited this long, we can wait an extra couple of weeks ... But in the meantime, I'll start taking orders - watching those build up should help keep his enthusiasm high during the long days of work!

And now that all the 'back and forth' is done, I can update my spreadsheet to cover all the costs that we have incurred. In the previous version of this, I showed the numbers negotiated with the three workers, but can now update that to include the additional expenses since then. The printing fee previously arranged was a 'per sheet' fee for the complete job, but Tetsui-san must be paid for these proofing days too (that is always considered a separate part of the job, and is even sometimes done by another printer). And both Sato-san and Seki-san have to be paid for the time they spent in the various meetings and consultations.
So our chart now looks like this (this is all in yen of course):
Confirmed expenses for initial batch of 200 sets | |
---|---|
Supplies | |
- Printing paper | 46,000 |
- Wood blocks | 20,000 |
- Packaging | 20,000 |
Labour | |
- Designer's royalty (10% of retail) | 70,000 |
- Designer's extras (consulting, travel, etc.) | 16,000 |
- Carver's fee (15% of retail) | 105,000 |
- Carver's extras (consulting, travel, etc.) | 24,000 |
- Printer's fee (25% of retail) | 175,000 |
- Printer's extras (consulting, travel, proofing) | 36,000 |
Total | 512,000 |
So it looks not so bad actually. That's a pile of money heading out the door now (about US$6,200 at today's exchange rate), and it will take all the revenue from the first 150 or so sets to recoup it. Just when that will happen I can't predict, but that's not really the point. Something beautiful exists that wasn't there ten weeks ago, and these three people have had some paid work - very welcome for them indeed - and a very valuable experience to boot. As I wrote before, it's win, win, win all around ...
And all of us heartily thank you for your support!

This thread continues here ...
Added by: Marc Kahn on April 25, 2011, 11:45 am
I'm curious about the designer's royalty (10%), carver's fee (15%) and printer's fee (25%). Are these well-established standards for the industry, or brand new standards in keeping with the Mokuhankan business plan?

Added by: Dave on April 25, 2011, 12:17 pm
A lot of this has just been pulled out of a hat. Payment for these three jobs is generally calculated differently.
Designer: no rules here. Remember, this 'market' - people designing for woodblock prints - no longer exists. All I can do is go by the kind of precedents existing for book authors, etc. From my own experience having books published (the colouring book etc. a few years back) I learned that 8~10% of retail is the common range for author royalties here. Famous people can command a bigger %; unknowns take what they can get.
So when I was doing my spreadsheets, I settled on 10% as being a figure that would be manageable from the publisher's end, and which should be acceptable to any designer.
Carver: for carvers, there are never royalties. And in fact, now that I think about it, it is quite possible that this is the first time in the history of woodblock printmaking in Japan that a carver has ever done a job on that basis. Actually, as we stand, with only the first 200 committed to production, he's not getting paid all that much. He hasn't complained about that, because he is very inexperienced and is happy to have anything, especially work that looks like 'real' work, and not something too simple.
But XX months from now, when this batch is sold out, and I send the blocks out to somebody for re-printing (if!), he'll be getting another payment (I'm thinking of 7.5% as a 'followup' royalty), and at that point he simply won't believe it. (I've of course talked about this to him, but from his point of view, it's kind of Dave's 'fantasy' idea; never, ever, has a carver ever received such an 'unnecessary' payment.)
Honestly speaking, putting this policy in place is going to be a burden for Mokuhankan as it grows, because those payments represent quite a loss of future profit. Printing from old 'free' blocks can be like printing money, in the case of a popular item. But I want the carvers to be full partners in the process, and I also want them (speaking of the future) to be very eager to accept our work, and to do a good job with it.
Printer: this is the most difficult. Nobody but nobody will talk about what they have been paid for anything, and getting real information is very difficult. Remember, I'm pretty much an outsider on all that stuff; I know dozens of the printers (I'm a member of the craftsman's association), but I have never shared in their work. Some of their work is open and shared, with everybody getting an even slice, and some is individual, with none of them being willing to let the others know what price they agreed to.
So I've approached it from the 'bottom up' - looking at the job, calculating the hours/days it should take, and setting the % at a level that seems like a reasonable amount for the printer to earn. That's a basically sound idea, but breaks down in the case of this project because the price is so low (for the work involved). It came out at 15 impressions during our final proofing the other day, and that's simply too many for 875 yen (which is what 25% of our retail price works out to.)
As far as I can tell so far, Tetsui-san seems like an 'average' printer - speed wise. No slouch, but not particularly zippy. First guess on the time it will take for 200 sheets of 15 impressions will be somewhere around 14 working days. Based on a national average of 22 working days per month, he should thus be getting about 2/3 of a typical person's monthly income for this job. (Assuming a woodblock printer is 'worth' as much as anybody else.)
Statistics I have here from the tax office put an average income (in the manufacturing sector) at 350,000 per month. 2/3 of that would be around 230,000. So this job is falling under that target level, and that's why - when the three of us were working out the colour separations - each time it became apparent that we would need 'one more block', Tetsui-san got pretty quiet!
This print set 'should' thus be around 4,500 yen. But that's over $50 ... and I think it would be a hard sell. But we all realize that we're making an experiment here, and trying to get something off the ground, so everybody is cooperating, especially Tetsui-san. (And to help smooth it a bit for him, I did actually 'up' the amount for the extras you see in that chart, paying him well for the day spent here working on sizing, etc.)
What would save our collective asses would be a strengthening of the $ vs the yen. If it would get back to where it was a couple of years ago, we could get our 4,500 yen with a dollar price of around $40. But there's no sense making our business plan based on 'wishes', 'cause it clearly isn't going to happen. And as it gets worse - as the $ declines ever more over the coming years, as seems inevitable - our little 'internet' business model may completely collapse. If that happens, we'll turn our attention purely to the domestic market, design the prints based on what we think will attract people here, price them appropriately, and treat anything we get from overseas as purely 'bonus'.

Added by: Margaret on April 29, 2011, 1:01 pm
Does Tetsui-san use a plastic baren? I don't see a barengawa.

Added by: Dave on April 29, 2011, 1:28 pm
Add Your Input