« How are we doing? Part two ... | Front Page | The Wood Question ... »
How are we doing? Part three ...
Posted by Dave Bull on April 30, 2016 [Permalink]
OK, here we go with the next instalment of our update, and as I mentioned in the previous post, we are encountering some major problems with our materials.
Let's start with the easy one - woodblocks. The background is simple to lay out for you: up until late 1998, I (and all the other carvers in town) were using cherry blocks prepared for us by Shimano Shintaro, who was the last hangi shokunin (block craftsman) in town. Late that year he died unexpectedly of stomach cancer, much younger than anybody had expected, and we were all suddenly faced with a real crisis.

Within days of hearing that news I was on my way to the wholesale lumberyards in a search for some cherry wood. I knew that I wouldn't find any 'ready to use', but felt that I had to get started on finding some. (I wrote about this on this old web page years ago.) As it turned out, it wasn't necessary for me to use the planks I purchased that day, because Shigeru Matsumura (the man who runs 'Woodlike Matsumura') stepped up to the plate and began to sell blocks of a laminated construction pattern - cherry wood facing on a strong plywood core.
Since that time, we carvers have been using his blocks, but over time they have become less and less satisfactory. His main customers are people making prints as hobbyists, and they are using shina plywood. He gets very little in the way of business for cherrywood; it's a sideline for him.
Shimano-san had a pipeline through the lumberyards up to the guys in the countryside who could search out suitable trees for woodblock printmaking. Matsumura-san is not part of that world, and indeed, the pipeline - the supply chain - is now long gone. There are now no longer any men with the knowledge of what makes a particular tree suitable for this use. Matsumura-san is just using cherry milled for furniture makers, and their requirements (mostly quarter-sawn straight grain) is diametrically opposed to what the woodblock carver needs.
So I don't intend this as an insult to him or his business, but the wood we have been receiving from him in recent years has become unbearable. Our young carver Kawasaki-san thinks I've lost my marbles when she sees the blocks I send her to use for our Portraits prints; it's wood that would have been suitable for nothing but the stove back when Shimano-san was around.
And then when the carved blocks get to the printing staff, they too look at me ... "Is this the best you can find? Really?" The grain patterns show in the print, there are uneven spots here and there, it doesn't absorb the moisture in the proper way ... in a word, the stuff is just junk. There is no other suitable term. It makes their work so much more difficult! And what makes this whole situation worse is that they've recently seen such nice wood - the old blocks from Doi Hanga - so they have fresh experience of what this stuff should be like!
What to do? Staffer Lee-san and I need to get out to the wholesale lumberyards, dig around to try and find some raw material that looks like it might work, then figure out how to get it sawn in the orientation necessary for our needs (at 72 degree angles around the log - a pentagonal pattern that will be very difficult to persuade a lumberyard to take on), how to dry it properly (how many years will that take?), then how to dress it down to proper thickness, where/how to find a hydraulic press to bond it to a core, what kind of adhesive to use, how to get the resulting blocks basically planed, then how to get them surfaced to the proper mirror finish ...
And only then - only when one of these blocks is on my carving table ready to cut - will I know whether or not we have selected a good log! If not ... it's back to the beginning. And even if it does turn out to be suitable, we then have to find the next one, and the next one ...
It's a solvable problem ... given enough resources, namely time and money.
Hah! Like I have any of either of those two things left ...
Anyway, enough warmup, let's get to the main point of these recent posts. I have to bring you up-to-date with a situation that can really only be described as an existential crisis for our venture.
It's our printing paper. I'll try and tell the story as concisely as I can, but I do have to give you a fair amount of background too, so you can get a sense of how this has been playing out.
The paper we use is the washi known as Echizen Hosho and it comes from one small geographical area of the country, and indeed, one small village, up in Fukui Prefecture. They have specialized in this paper since way back in the Edo period (longer, actually), and it is this paper on which most of the classical high-quality ukiyo-e were printed. (Lesser quality paper was of course used for cheaper editions, but hosho was the unequivocal choice for good work.)
But with the gradual decline in traditional printmaking over the course of the 20th century, the number of workshops in that village declined steadily, and for the past couple of decades, there have been only two families specialising in this work.
One family, the acknowledged 'leader' in the field - and whose head member has been named a Living National Treasure (as was his father before him) - has supplied all my paper for the past 25+ years. We use no other.
Now the paper as it comes from their workshop can't be used directly for printmaking. It must first be sized with a glue mixture to give it enough strength to stand up to the vigorous treatment we give it during the printing process. That has traditionally been done by a specialised craftsman, and during the entire time that I myself have been active in this field here in Japan, all of this work has been done by a single person, as all the others retired as the volume of work decreased.
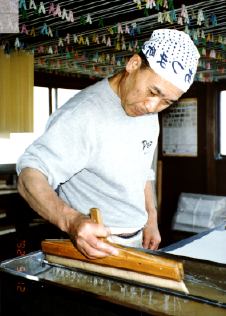
I had no complaint with his work, but sometime back between 5~10 years ago, the quality of the sizing declined. There were cases when an entire batch was badly done, and other times when the quality within a batch was extremely uneven, making the printer's work very difficult.
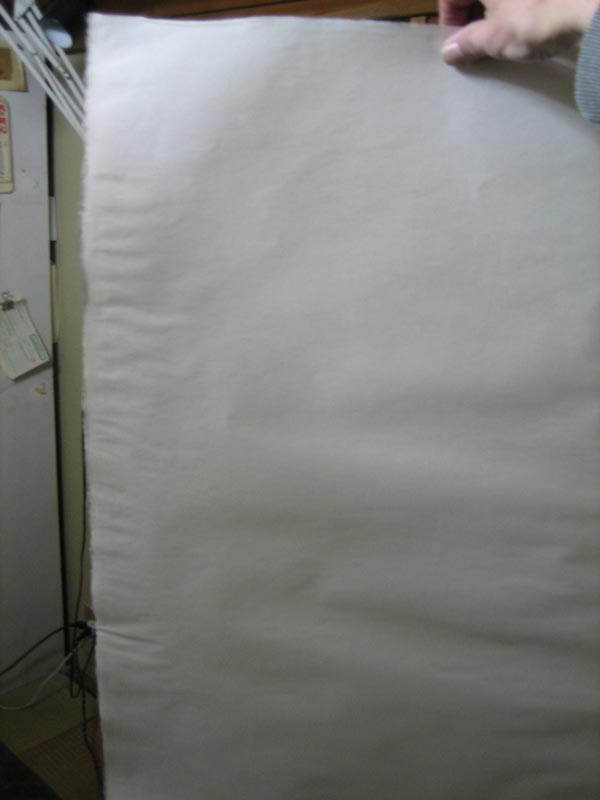
Given this trend, plus the fact that there was only one man doing it (and elderly, to boot) I decided to try and learn how to size the paper myself. I won't recap that entire project here, but there are a number of posts over on my Woodblock Roundtable that cover the progress I made. I wasn't very good at it at first of course, but did gradually get better, and in recent years sizing has no longer been an issue for us; I have become quite capable of producing decent results.
Until last fall.
My printers - all of them, both in-house and the professionals working at home - began to give me feedback that the recent paper I was providing to them was sized quite weakly, with the surface fibres easily pulling up while printing.
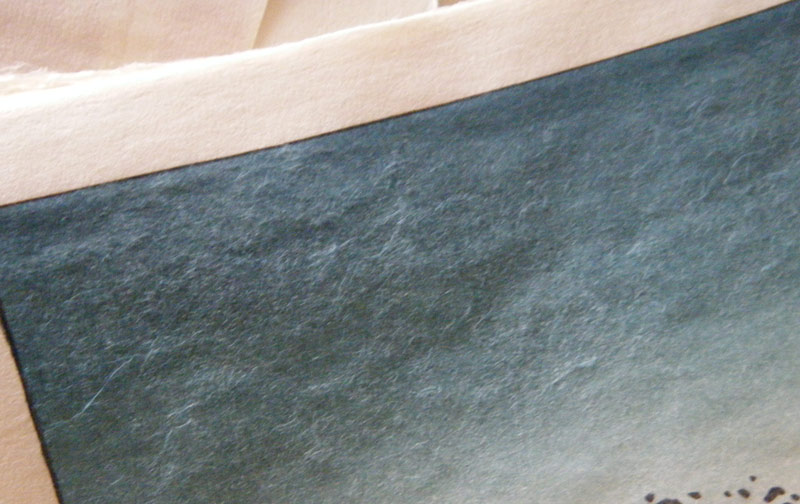
Everybody involved, all the printers as well as myself, assumed that the problem was me. Although I had been gradually getting better at this, applying size is an extremely complicated job; the amount of glue in the mix varies with the season and the humidity in the air, the depth of application needs to be different depending on the particular job at hand, and the glue itself varies from batch to batch. There is nothing trivial about the work at all, and my lack of experience seemed to be the problem.
I responded as well as I could to their suggestions, increasing the glue level and/or the saturation, but the problem continued. The more experienced among the printers could sometimes get the paper under control, but our in-house printers lost a huge number of prints to bad paper.
The situation became critical in January, when our most experienced printer, Kubota-san, lost two entire batches of the Great Wave (60 sheets in each batch) to 'poor sizing'. The publisher normally doesn't pay the printer for rejected sheets, but given the uncertainly about the roots of the problem - was it really my fault, or his? - I had to pay him for all those prints even though they are unusable.
But as we moved into spring, and the weather warmed up, making it easier to apply size to the paper, things didn't get better, they got worse. But there was an interesting development - we heard from our printers that they were encountering the same problem with paper from other publishers as well, paper from that same maker, but which they had either sized 'in house' or sent out to that same sizing craftsman.
I finally thought it might not be a bad idea to talk to the paper maker about this, so called them up, asking - not accusing - whether there had recently been any changes in their material or procedures. I explained that I was having a great deal of difficulty with the paper, and was starting to wonder what was different. The man I spoke to, the son of the 'national treasure', denied any change at all, and when I suggested that other people were encountering problems, he said that he had heard nothing at all from anybody ...
But no more than a day or so after that phone call, I was speaking to a young junior printer who works at another shop (perhaps Japan's most famous traditional publisher), and as we compared notes on this problem he mentioned that because they were having such trouble with the paper, his boss had taken a trip recently up to the paper maker's workshop to discuss the issue ...
Hmm ...
So here's where things stand at the moment:
- something fundamentally structural has changed in the paper. It's not just a question of raising the 'strength' of the nikawa sizing to stop the fibres pulling up. With too much nikawa the size simply won't blend properly into the sheets, and they become impossible to print.
- we have now talked to a number of other people (printers/publishers). Without exception, all are having the same trouble. All fingers are pointing to the same place ... something has changed in the paper from that particular workshop ... Whether it's the raw materials, or their procedure, none of us can say.
- Ayumi-san has been sent home for a while; we have no paper on which she can make prints ...
- Kanai-san has been told to wait until we can find some paper for her ...
- Kubota-san - with whom I have a gentleman's agreement to guarantee at least $3000 worth of printing work every month - has had nothing from me for months ...
- our other printers have been working on whatever scraps we can scrape up from older stock ...
- the Doi Hanga project is of course completely on hold; YouTube subscribers are emailing ... "When is your next video going to be ready?"
- we have the May and June subscription prints in the Portraits series ready, but no paper for more ...
- I am sitting on more than 1,300 sheets of unusable paper, for which I have paid well over $17,000 ...
- the papermaker denies any problem ...
The workroom upstairs is strewn with all the samples and test batches that I have made over the past couple of months, as I repeatedly try to find a particular 'recipe' that will bring this paper to useable condition.
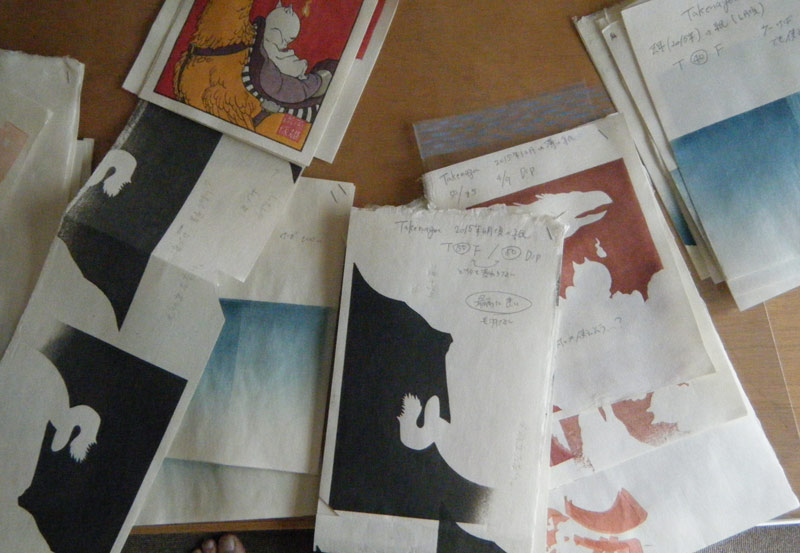
We even sent a batch of paper - anonymously via a third party - over to that same sizing craftsman I used years ago; minutes after it came back, two of our printers eagerly tested a few of the sheets ... feathering everywhere.
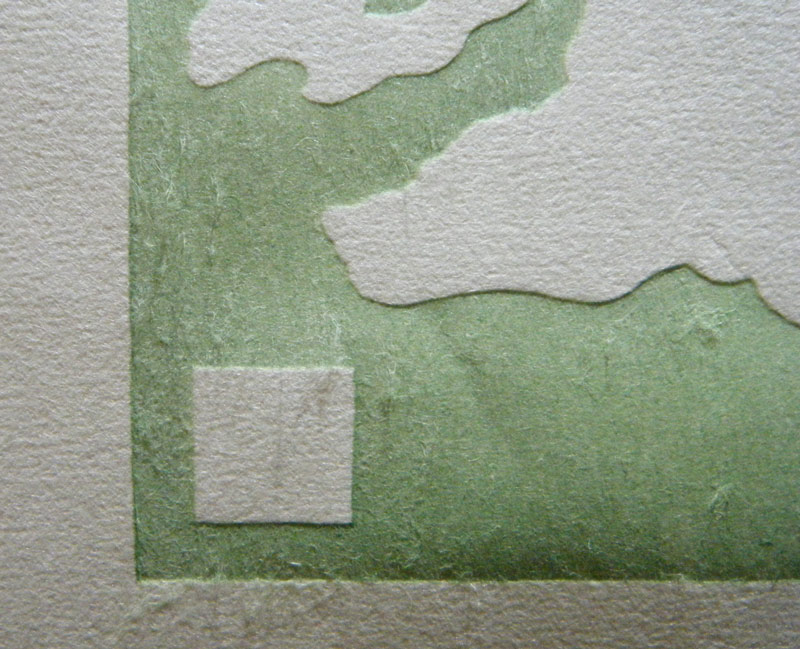
All this has been taking place in the environment of the Asakusa madness of the past couple of months. I've done X number of Print Parties and dealt with all the visitors each day, then headed upstairs in the evenings for more sizing tests.
So. What I am going to do?
Well, long term, I know what to do. Paper making per se is practiced all up and down the length of this country. Very few of those papers are suitable for the physically intense procedures of traditional printmaking, but it seems to me that if I could find the right workshop/person, I could work with them to adapt one of their papers to our requirements, or even better - convince some eager young person to take on the challenge of re-creating the wonderful kind of paper we used to have back in the old days. It wouldn't be easy, and it would take years, but it would be doable I think.
That doesn't help me though, in the here and now. I have collectors around the world waiting for our prints. I have printers who need work to pay their bills. I have blocks galore ...
But I have no paper, and no prospects of getting any.
It has been a long time indeed since I found myself in a situation where I simply don't know what to do. Whatever problems have arisen in recent years were all solvable with a 'Plan B' approach, or the application of enough hard work.
Anyway, enough for tonight; I have to get back upstairs ... I'm going to try some tests this evening by dipping the paper sheets into the sizing mixture, rather than brushing it on. Perhaps that will give this defective paper enough 'body' to print properly without feathering.
I'll keep you updated ...
Added by: Stu on May 2, 2016, 10:41 am
Wow...
You're right... those are some major challenges. The paper, in particular, seems to be the most significant, but if it also affecting the other 'big players' in the printmaking/publishing craftsman community, perhaps there could be some way to work together to more quickly mature alternate sources.
As for the cherry blocks, perhaps this is something that could be obtained outside Japan? While the cherrywood itself would be different, might there may be artisan-oriented mills in the US, Canada, or Europe that might cut local, dried cherry to your specifications and bond it to a substrate?

Added by: Grahame on May 2, 2016, 10:45 am
Dave,
I'm very sorry to hear all the issues you're having. I know when I visited in March, you had mentioned some of these issues but it seems even more have cropped up in the last month. I hope things improve soon.
é ‘å¼µã£ã¦ãã ã•ã„。 

Added by: Tom on May 2, 2016, 1:07 pm
We all knew that materials have have been getting more shoddy but to reach a point where woodblock prints can no longer be made in Japan is really a national emergency. This should be front page news. I think the issue with the blocks might be solved by making your own plywood, For my small editions I have been happy using my own American cherry faced ply which I had made up as a more economical substitute for solid cherry. I used a lightweight African timber Obechi as the core and this makes the task of bulk carving very easy indeed. I do admit that these blocks are not as robust as the solid blocks, but they do not fall apart as one might fear. The real problem is sourcing veneer of sufficient thickness. I think perhaps a special order is required to have the thick veneer made, the rest is easy. The problem with paper may be insurmountable, but if an answer lies in China I will not be surprised. A sad state of affairs. I am hoping your ingenuity will win through yet again. Fingers crossed.

Added by: Bob on May 2, 2016, 1:51 pm
I have been making my own blocks for some time using black cherry from the east coast (1/8" thick lumber also known as thin lumber in the trade. There are a number of internet sources.) that I glue onto a Baltic birch plywood base. Supposedly the black cherry and the mountain cherry of Japan have almost the same specific gravity, but since I have never had the opportunity to work with the mountain cherry of Japan I don't know if the carving characteristics are the same or similar. If you would like, I would be happy to send you a block for you to see if it would meet your needs.

Added by: Mike B. on May 23, 2016, 5:47 am
As Stu alluded to, this sort of situation seems like what trade industry associations are for. Surely it's in the interest of all serious publishers to have reliable sources of materials. To speak with one voice when dealing with suppliers, to pool money for custom lumber orders, to talk to the press and the government about the gravity of the situation.
I understand why you don't have the time to organize this, but I'd kind of hope someone else would step up, rather than everyone struggling individually with these issues.

Added by: Dave on May 23, 2016, 2:10 pm
Surely it's in the interest of all serious publishers ...
Interesting point ... why aren't we hearing more voices raised about this? Where's the feedback/complaints from other publishers, like the people making those Star Wars prints, etc. etc.?
There's a Japanese word - shoganai - 'can't be helped'. Most of the other craftsmen in this field have - right from the time they were youngsters - lived in a time of long and slow decay. All their lives they have been faced with the (to them, inevitable) fact that the end is near, and that this craft will fade out. To put it most simply, they don't/won't/can't fight back. It's just shoganai.
I'm not Japanese. That's both a plus and minus ... but one big difference is that I refuse to accept that word into my vocabulary. It's perhaps kind of pretentious of me to behave this way, and maybe even a bit melodramatic, but we're just not ready to give up on this stuff.
Anyway, the main point to reply to you, is that from here on in, we're pretty much going to be dependent on our own resources for solving these problems.
(And we have made progress on both fronts: paper and wood; I'll be posting soon ...)

Add Your Input