« Mokuhankan Partner news ... | Front Page | Knife set - sourcing the cherrywood »
Knife set - handle prototyping continues ...
Posted by Dave Bull on February 15, 2012 [Permalink]
There is a problem to be faced with this kind of prototyping project, and that is with the selection and use of tools and jigs. These little handles are simple in concept, but not so simple to fabricate; none of the faces are square, and they are too small to easily hold for cutting, shaping and sanding.
Now of course in a commercial production situation, things like this are made on custom jigs, so there are no problems at all in handling and cutting the pieces. And I will indeed be designing and building such jigs to do the work as efficiently as possible. But the kind of Catch 22 facing me at the moment is that until the design is finalized, I cannot begin to make such jigs, but without having some samples in hand, I can't finalize the design.
That's what prototyping is all about, making a bunch of one-offs in differing patterns, in order to work out your final design. So I'm having to make some 'prototype jigs' too, because I certainly don't intend to try cutting such tiny pieces on my giant table saw by pushing them into the blade with my fingers!
Here's an example: each of the 'blanks' we saw in a previous post needs to be sliced at an angle into two pieces, resulting in two handles. This is the prototype jig - the crossbar is bent under the white plastic drawer handle, and clamps the piece firmly in place as the wood passes into the saw.

Giving us the two pieces cut at the correct angle:

But for the next two, I might want to try a slightly different angle, so have to 'jimmy' the position of the jig on the saw table surface. I suppose I could have made a more elaborate jig, that would allow delicate angle adjustment, etc., but how much time can you spend on jigs that will be tossed aside next week?
Here's an overview of the table saw, by the way. I made it back in 1987, when I was seriously thinking of setting up a professional toy making workshop, after getting many orders from local people - "Can I have one?" - for the toys that I had made for my own kids at the time ...

I also made a jigsaw and disc sander, which is certainly showing its age:

And the overall scene:

... no workbench unfortunately. That has been co-opted by the ladies downstairs, for print packaging and other related work.
I bring this up today, because last night I had to finally figure out which way to go with this tool thing. These old tools of mine have served me very well over the past couple of decades, and I tell you it's a pretty nice feeling to have things in my life (those kids' toys, various things in my print workshop, furniture, etc.) that I made myself using tools that I made myself.
But for the pretty substantial jobs facing us over the next couple of months - the production of a large number of very finely made 'parts' for these chisel handles, the boxes for them, and of course the upcoming job of making all the cases for the 'Arts of Japan' subscription prints - I have to admit that these tools are not really suitable for the work. My table saw is very heavy duty, but simply does not have the accuracy we are going to require.
And, many of the steps in the production will require a kind of cutting that I can't do with these tools, for example, slicing a thin top off each handle to make the opening into which the blade will fit. Using this table saw would cost around 3mm of wood - far too much loss. I need a band saw.
So, I did some shopping around ... and run into the next kind of conundrum ... I live in the wrong country for this kind of thing!
Countries where there is a flourishing DIY/garage-basement workshop culture are flooded with all kinds of tools. You need a good table saw? No problem; you have an extraordinarily wide choice, from cheap imported junk, right up to massive units being decommissioned from a closing factory, and everything under the sun in between.
Here in Japan, where there is next to no DIY culture, and where nobody has a home workshop (who's got the room for it?), we have only the 'outer' two options: tin junk for hobby use, or huge units from the latest round of factory closings, as the final remnants of our manufacturing base shut down for the move to China/Vietnam/Cambodia/etc..
So I really don't have a lot of choice in how to equip my workroom for this project. I searched for used tools as well as I could, but found next to nothing that is useable/attainable. So over to Amazon.co.jp, and make a selection from the El Cheapos.
These four will be delivered here tomorrow:
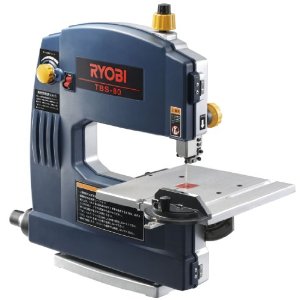


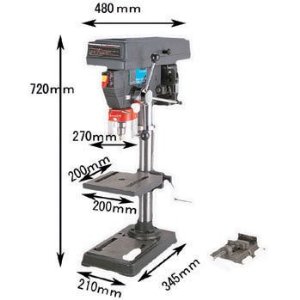


Total bill: 91,000 yen (about $1,100). Life expectancy? Well, at age 60, I'd expect that any tools I buy at this point would outlive me, but there is no way that will be the case with these ...
But I hope they'll last at least long enough to get the first batch of handles (and cases) made!
Added by: G. Jarvis on February 16, 2012, 1:16 am
I Know the problem.
The inexpensive Chinese drillpress has held up well and still going strong. But I am on my second cheap tablesaw (motor bearing failure, cheaper to replace than repair) and my second cheap belt sander. Drive belt failure is the sander's problem. The first one was replaced when replacement drivebelts became unavailable. I replaced it with a Ryobi that has the same problem, but parts are available.

Added by: Dave on February 16, 2012, 1:26 am
Added by: Sharri on February 16, 2012, 2:58 am
I guess I'm lucky that I have a lot of Dad's tools. My drill press is circa WWII, or shortly thereafter. It is big, heavy, a brute, but it is the machine that never gives up! Likewise for saws, sanders, grinder and more. However, like you, I have no workbench. Still waiting for that..

Added by: serge on February 17, 2012, 12:42 am
Looking at your prototyping problem, you may want to consider the new 3-d printing services. 3D printing is now quite cheap (basic 3D printers are below $10,000) and you have load of companies offering this service on the basis of a simple drawing. What was expensive prototyping is now much easier & cheaper. Once you get the model right, you can then move to "production" using all the equipment you just bought....

Added by: Dave on February 17, 2012, 1:12 am
Well, when I say 'prototyping' I don't really mean the 'design' of these handles - that is (roughly) set by tradition and function. What I am prototyping is the process of making them, and that's not something that a 3-D printed sample is going to help me with ...
I did say 'roughly' though in that sentence. In fact, our design for these handles is somewhat unique, and these chisels will be instantly identifiable on first sight. There is nothing anything like them on the market. (Although Sato-san and I are quite curious about what might happen over the next few years - whether or not anybody will try and duplicate what we are doing ...)

Added by: George Jarvis on February 24, 2012, 11:44 am
Sorry I've no direct experience with the Ryobi
Thickness planer. When I have need of one I visit
an eighth generation Buddhist sculptor (busshi.com)
and use his which is ancient and weighs a couple of tons.

Add Your Input