« Another _Big_ Step! | Front Page | Knife set - next step »
Knife update ...
Posted by Dave Bull on January 28, 2012 [Permalink]
I spent the day in Tokyo yesterday on Mokuhankan business (partially), and can report some progress on the new knife set.
First was a stop at one of the shops selling/making paulownia boxes. Given that this new project involves so many things that all have to be up and running before we can get the product on the market, Sato-san and I thought that it might be a sensible idea to use a ready-made box, if we can find a place to supply them at a reasonable quality and price.
The people I spoke to in the box shop took down my description of what I want, and will get back to us next week with a quote. The stuff in their shop looks to be a good quality, and we'll see what kind of price they will give us.
Another option on the table is for me to make the boxes myself, and as I am going to be tooling up next month to make boxes for my upcoming print series, we may indeed end up going that way. We'll see ...
But a more important decision we made yesterday was on the fundamental design of the chisel handles. We met up at the restaurant where the craftsman's association was having a get-together, and during the dinner (we sat next to each other) we snatched bits of 'private' conversation where possible ...
First, let me show you a snapshot of a couple of the chisels in my own toolbox:
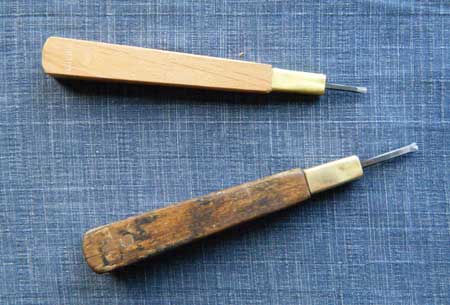
These are aisuki, the blunt-nose chisels used for general clearing near the lines. The top one is fairly new (unused yet, actually) and the bottom one has been with me since almost the beginning of my printmaking, being purchased in Tokyo in (I think) early 1981.
For those of you who have no experience with these, this next photo shows how they 'work' - the brass sleeve comes off, and the handles (which are a single piece of wood split in two) open to reveal the blade in its slot. The theory is that the blade can be replaced once it is worn out (from becoming just too short through repeated sharpening).
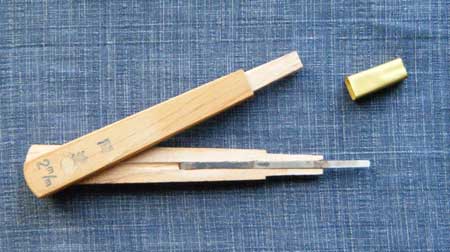
Now that's a nice theory, but in real life, these chisels wear down so slowly, that replacing the blade becomes a purely theoretical matter. The blade in that lower chisel is still the original one. (Note that this is not true for the main carving knife - I replace that one in the space of months ...)
So given that the blade really doesn't need easy/quick access, professional carvers here do not use handles with the brass sleeve. Here's another of my chisels, with the sleeve tossed away many years ago, and cord being used to keep the thing together. (You can see the shape where the handle was cut to receive the sleeve ...)
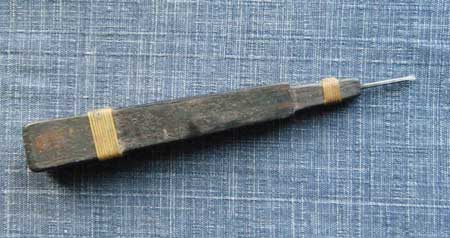
Now let's take a peek into a traditional carver's toolbox. This is a snapshot of some of the tools belonging to Motoharu Asaka (about whom we will read in my upcoming newsletter) (click for a closeup):
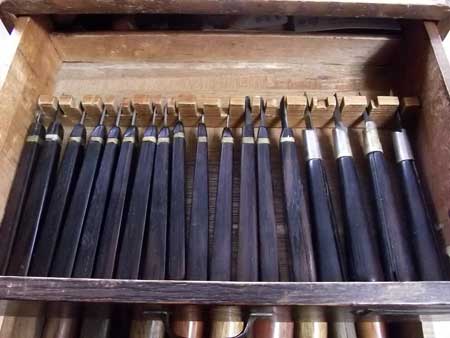
No sleeves at all (on the chisels). All tied with the cord.
So ... given this background, Sato-san and I had to come to a decision with our new chisels. Go with the 'modern' sleeves, or use the traditional pattern?
There are various pros and cons:
- Modern - plus
- sleeve is easily removed, making blade change easy
- this is what people have come to expect
- Modern - minus
- the sleeve falls off in times of dry humidity
- the sleeve can sometimes bang the work, causing chipping
- the presence of a sleeve is (in some ways) an indication of a lower quality item
- Traditional - plus
- no sleeve to cause problems (banging the work, falling off, etc.)
- easier to hold, with no interruptions in the shape of the handle
- a generally 'high class' appearance
- Traditional - minus
- more trouble to change the blade (the owner may not know how)
- may be resisted by consumers, who have come to expect the brass sleeve
We tossed these points around and came to a unanimous decision on which way to go. Given that we want these tools to be the highest-quality, most attractive ones on the planet, we're going with the cord. No sleeves. Potential purchasers have advance warning - get your fly-tying skills in shape! :-)
Now of course, we are not going to leave you on your own. First is that each of these sets will have a pocket in the lid of the paulownia box, in which will be a small booklet, along the lines of a typical CD booklet. This will have background information on the tools, and of course plenty of information on care and maintenance, including instructions on how to tie the cord. And we're thinking of one more step - if we can figure out how to design it, we'll add another small pocket, and in there will be tucked a small coil of shamisen string of the proper gauge, because - yes indeed - that's the material of choice, and we rather doubt you will be able to find it at your local corner store!
(Of course it doesn't have to be shamisen string - the kind of cord fishermen use to tie their flies is also perfect for this. It's very strong for its weight, is resistant to coming untied, is cheap, and is available anywhere.)
Now with that decision behind us, what's next? Well, Sato-san has asked me to meet him at the knife workshop on Tuesday morning. It seems that they have something to show us!
Added by: Linda Beeman on January 28, 2012, 11:58 pm
I like this idea a lot Dave. I never thought of Michigan as "dry" but those little sleeves come off my tools all the time. I put little pieces of wood chips in them to try to keep them on.
Can't wait to see them when they are done!

Added by: Marc Kahn on January 29, 2012, 4:07 am
On your "Table of Contents" web page, there is a picture of you about to strike a chisel with a wooden mallet. Are the chisels that you're going to make in this project designed to be struck like that, or with the pressure applied by hand?

Added by: Barbara Mason on January 29, 2012, 5:27 am
Dave,
I am not as resourceful as those carvers that use the cord to wrap their tools, when I lose the little ferrule (it happens when you cart stuff around in teaching) I use white artists tape to keep things together, and it works well. Also the tape wrapped tool lets folks know it is mine and not theirs...I do let students use them.
I have never replaced a blade...so think there is little need for that except maybe on the knife....
However the idea of having two blades and one out to be sharpened is something I had not considered and might think of, being a basically lazy person. I hone them, but sharpening them is pretty tedious....and have had students take a pretty good chunk out of one a time or two.
Barbara

Added by: Tom Kristensen on January 29, 2012, 6:32 am
Yes Please! I'll take a set.

Added by: Dave on January 29, 2012, 8:08 am
Are the chisels that you're going to make in this project designed to be struck like that, or with the pressure applied by hand?
There will be no 'striking' chisels in this first set. We included discussions on a wider range of chisels with the maker, but we're going to hold off on those until we get this first project launched. That type of tool will actually be easier for us to produce, as the hammered chisels used by printmakers do not differ in essentials from those used by other types of woodcarvers (and even carpenters).
sharpening them is pretty tedious...
Barbara, you must be doing it wrong! :-) In any given day of work, I spend no more than a couple of minutes sharpening. These tools are so small, they cut down extremely quickly (on a good stone), and time is not the problem ... accuracy is!
I'll take a set
Get in line, Tom!
Well, it's not actually such a long line at this point. These tool sets will have a label inside to identify them, and on that label will be the name of the person who ordered that set, along with the date of manufacture, and a 'serial number'. At present, it looks like you'll get set #2 (if you do go ahead and order one when the order page is open), as one other person has already said "I would like to put an order for a set in."
Interestingly, he also added, "I am also willing to pre-pay, if that were to help by any means to defray whatever start-up costs you may be incurring."
To his pre-pay suggestion I replied, "I'm certainly not going to ask for any money at this stage - we haven't even seen any steel yet from the blade makers ... so that would be kind of premature. But I'll keep you in touch with how it is coming along."
This kind of early enthusiasm and support is very encouraging; thank you!

Added by: Tom Kristensen on January 29, 2012, 10:49 am
I am not unhappy with the Baren Mall chisels I have been using for the last 8 years, and as you point out I'll never be able to wear them out - and I am one who sharpens pretty aggressively using a Tormek wheel. But, I just know that a sharper edge will be a revelation. Even a small gain in sharpness is worth the investment, given the thousands of hours of carving ahead.
Having said all that, I would also like to improve my sharpening technique. I have ordered a few stones in my time, but I have never been happy with them, either too small or possibly incompatible with my steel. Would there be any possibility of matching these new tools with the right stone(s) for fine sharpening. Again an investment I would jump at.

Added by: Dave on January 29, 2012, 11:00 am
any possibility of matching these new tools with the right stone(s) for fine sharpening?
Absolutely. This is already on our list, as soon as we get some of these blades in hand to test.
The 'problem' with stones, is that they are pretty heavy. And if you use just a little one, it's difficult to make good long smooth strokes ...

Added by: Dale on January 30, 2012, 11:44 am
I'd like set #3 please! And good stones would be a great investment...and if by chance you can put carving skills into the package, I'd like to go to the head of the line!

Added by: Dave on January 30, 2012, 1:52 pm
set #3 ...
Hey, you guys are getting crazy! I myself don't even yet know how much this set will sell for!
(I'm going to write something about that in the next post, a bit later this afternoon ...)
Bit it seems there is a point gradually becoming clear here - that trying to find the 'cheapest' solution is not always (if ever) the best way to go. Some of us (long time Apple customers, for one example) have always know this. The 'rest of the world' - going by Apple's astonishing numbers recently - is coming around!
Thanks Dale, for your vote of confidence too!

Add Your Input